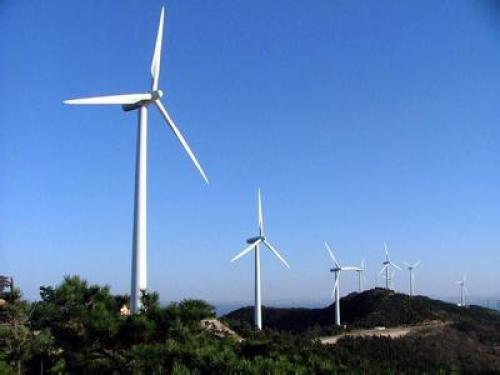
According to the "China Wind Power Development Road Map 2050" released by the National Development and Reform Commission Energy Research Institute, by 2020, 2030 and 2050, China's installed wind power capacity will reach 200, 400, and 1 billion kilowatts, respectively, which will meet 5% respectively. With 8% and 17% of electricity demand, wind power will become one of China's top five power supplies.
The anti-corrosion coatings for wind power equipment umbrellas will usher in a new milestone. It is estimated that during the seven years from 2013 to 2020, the gap in China's wind power coating is 130,000 tons, which means that there will be nearly 7 billion US dollars of wind power coating market.
Development of domestic wind power coating market The wind energy resources on our planet are very abundant and the development potential is huge. At least 70 countries around the world are using wind energy. Wind power is the main form of wind energy utilization. Under the background of national policy support and tight energy supply, the rapid rise of wind power equipment manufacturing industry in China has become the most active place for wind power investment in the world.
It is understood that the wind power industry in China has extended to inland regions such as the northwest and coastal areas. In recent years, the installed capacity of wind power in China has continued to grow rapidly. The development of wind power has driven the vigorous development of the relevant equipment market, and has also driven wind power coatings. The rapid development.
Due to the wide geographical location of wind power plants in China, the wind turbine system will encounter various kinds of harsh environmental erosion, such as sand, ultraviolet radiation, temperature difference, rain and snow, ice, etc. Especially for offshore wind power, it will be eroded by water vapor and salt fog for a long time. As a result of the impact of waves and waves, corrosion problems have occurred. Therefore, in order to ensure the normal service life of wind power equipment for 20 years, relevant protection measures must be taken, and coating protection is one of the important links. Wind power protection coatings mainly include tower anti-corrosion coatings and blade protection coatings, while tower bases, hubs, bearings, nacelle covers, fairings, and other electrical equipment also need to be protected by paint.
In particular, with the booming development of China's wind power industry and the complexity of the domestic wind farm environment, the technical improvement of anti-corrosion technology for wind power equipment has become an imperative. Fluorocarbon coatings have great potential in the future wind power market.
The introduction of the wind power anti-corrosion market in the future will greatly improve the weathering and anti-corrosion performance of wind power equipment, extend the period of equipment protection, and reduce maintenance costs. Compared with the polyurethane system coatings currently used in wind power facilities, fluorocarbon system coatings will undoubtedly become upgraded products. It will play a very positive role in promoting the upgrading of wind power coatings in China.
The full ceramic ball bearings listed below are supplied with rings and balls made from zirconium dioxide (ZrO2). These zirconia bearings are available as full complement (no cage) or with cages made from PTFE, PEEK or 316 stainless steel.
These are non magnetic, non-conductive and highly corrosion resistant to most chemicals although ZrO2 bearings are not recommended for prolonged contact with steam. Full complement bearings or those with a 316 stainless cage can be used up to 400°C while bearings with a PEEK or PTFE cage can cope with temperatures of up to 250°C. For temperatures below -70°C, PTFE or 316 stainless steel cages are preferred. Standard radial clearance for full ceramic bearings is C0 but other clearances can be supplied to order.
ZrO2 ceramic bearings are generally used for their extreme temperature capabilities, excellent corrosion resistance or non-magnetic properties. Other sizes can be supplied on request.
The Description of Ceramic Bearings:
Compared to steel, Ceramic ball Bearings have many specific advantages. They offer superior corrosion and heat resistance, higher dimensional stability, and lower density, which facilitate high speed. Ceramics are superior to steel in heat and corrosion resistance, and are lightweight and extremely hard as well. Consequently, ceramic rolling bearings can be used in environments where conventional steel bearings cannot. That is to say, the superiority of these bearings makes it possible that they can be applied in some special environments.
Firstly, they can be used in corrosive environments. Compared to stainless steel bearings, hybrid and all Ceramic Bearing lasted three and twenty times longer respectively. It is presumed that water readily adheres to silicon nitride and forms a better lubrication film, leading to extended bearing life.
Secondly, they can be performed in corrosive agents. Generally, silicon nitride has excellent corrosion resistance. However, corrosion resistance varies depending on the type and quantity of sintering additives, and certain corrosive agents decrease in hardness and flexural strength. In such situation, it is can be proved that the carbide-based ceramic bearings are the most effective.
Thirdly, they can be used in high-temperature vacuum. An all-silicon nitride Ball Bearing with a self-lubricating laminated cage (mainly composed of MoS2) and with MoS2-coated rings and balls proved superior in durability in a high-temperature vacuum environment. Compared with the hybrid bearings, the all-ceramic bearing was superior in both dynamic frictional torque and life.
Fourthly, they can be performed with poor lubrication. As ceramics are extremely hard and have outstanding wear resistance, they outperform other materials in bearing life without lubrication. According to a test, the steel bearing seized within a short period while the hybrid and all 627 Ceramic Bearings, though sustaining wear, did not. And the all-ceramic bearing sustained considerably less wear than the hybrid bearing, indicating that its endurance life is much longer.
Cermic Ball Bearing,Full Ceramic Bearing,Hybrid Ceramic Bearing,Self-Aligning Full Ceramic Ball Bearing
Shijiazhuang Longshu Mechanical & Electrical Equipment Trading Co., Ltd. , https://www.lsjgbearing.com